Cape Town-based Kobus Naval Design (KND) has launched a project aimed at developing boats from high-density polyethylene (HDPE) materials. Strong, safe and easier to maintain, the boats are ideal for inland waterways to be used by fishermen or harbour pilots. KND is a beneficiary of the marine programme of the Aerospace Industry Support Initiative (AISI), a programme of the Department of Trade, Industry and Competition.
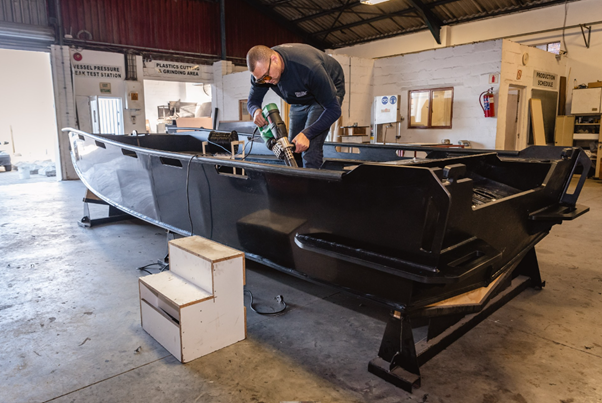
HDPE is a versatile plastic that can be moulded at elevated temperatures and solidifies upon cooling. Unlike aluminium boats, HDPE allows for easy repairs without the need for specialised welding equipment. KND is adopting the use of HDPE due to its numerous advantages. HDPE-developed boats are recyclable, capable of withstanding diverse weather conditions, require minimal maintenance and exhibit high resistance to corrosion.
Naval architect and Chief Executive Officer of KND, Kobus Potgieter, explains, “The primary aim of this project was to innovate within the marine industry by leveraging HDPE’s unique properties to create boats that are durable, environmentally friendly and cost-effective compared to traditional fiberglass counterparts. Our motivation comes from recognising HDPE’s potential to revolutionise boat manufacturing processes and product offerings.”
“HDPE’s high resistance to corrosion, impact and marine biofouling presents a significant opportunity to enhance the longevity and sustainability of marine vessels, addressing ecological concerns and the demand for more durable maritime solutions,” further explains Potgieter.
Numerous boats operate on African inland waterways. However, they are often underutilised due to expensive maintenance and safety concerns that do not always adhere to expected standards. Most companies use steel or aluminium for boat manufacture, but this approach has several disadvantages. Steel boats require regular maintenance due to corrosion issues and repairing aluminium or steel boats require expensive welding equipment. Additionally, painting boats to prevent corrosion is a time-consuming process.
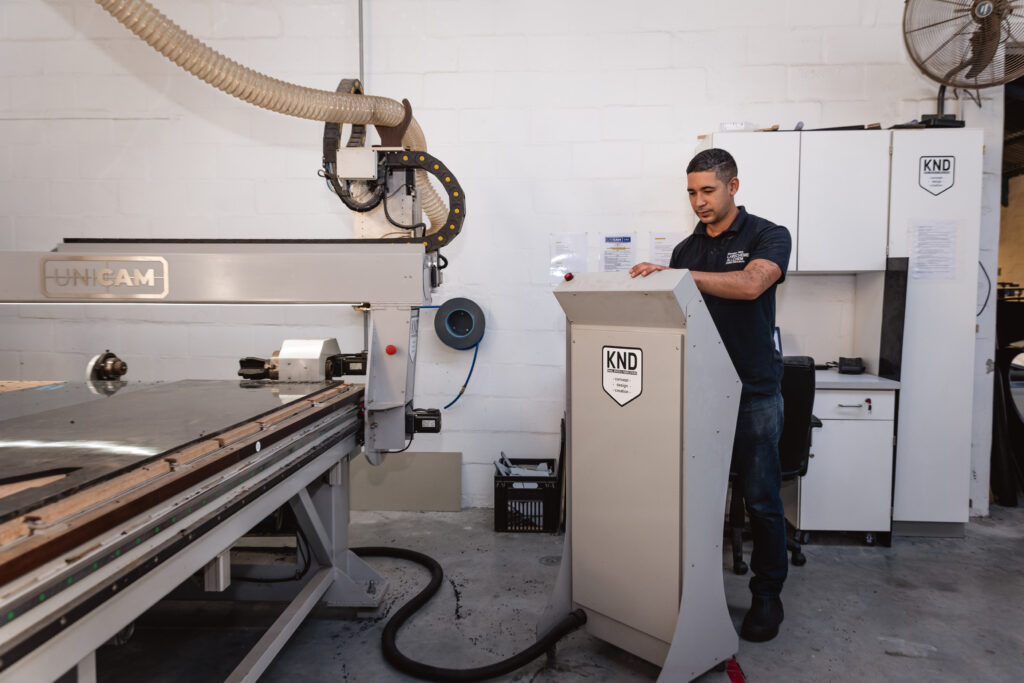
Employing HDPE in boat construction, KND undertook the tasks of design, manufacture and rigorous testing to ensure the boats’ reliability. Once the project is completed, the company will initiate the certification process for their newly developed product.
Throughout the project, comprehensive documentation of the design will be maintained – a crucial requirement for certification. Additionally, test reports generated during the testing phase will form part of the data pack submitted to the certification authority.
“We are finalising the design phase. The support from the AISI has been instrumental in advancing our HDPE boat project. Their expertise and resources have played a pivotal role in driving innovation and strengthening our confidence in achieving our goals. This partnership exemplifies how collaboration can lead to groundbreaking advancements in sustainable maritime solutions,” concludes Potgieter.
Marié Botha, manager of AISI operated from the Council for Scientific and Industrial Research in Pretoria, explains that the programme aims to support small enterprises by offering business advice or other assistance to bring products to market and improve their competitiveness. “Entrepreneurs often require product evaluation, testing or assistance with accreditation,” she explains. “Our initiative steps in to provide guidance and access to state-of-the-art facilities for these purposes.”
As with the KND project, the aim of this project aligns with the overall goals of AISI, which include accelerating localisation, facilitating skills transfer and promoting export opportunities. It aims to assist local companies in accessing international markets.