The Gauteng-based Impala Bolt and Nut expanded its toolmaking operations to offer locally produced South African parts to the market, reducing their reliance on imports. The company achieved this through the assistance of the Aerospace Industry Support Initiative (AISI) – a program of the Department of Trade, Industry and Competition that is driven by the Council for Scientific Industrial Research in support of local economic. Impala Bolt and Nut is a well-established and significant producer of bolts, nuts, washers and specialised fasteners for the engineering, automotive, construction and mining sectors.
Tooling production includes designing, cutting, manufacturing and polishing special materials used to create parts and components. Unfortunately, the South African tooling design and manufacturing capabilities have diminished in recent years, and downstream steel part production companies have limited abilities. This challenge increased the import of tooling from other countries, thus raising manufacturing costs. The knock-on effect of rising tooling costs has negatively impacted manufacturers trying to compete in local and export markets.
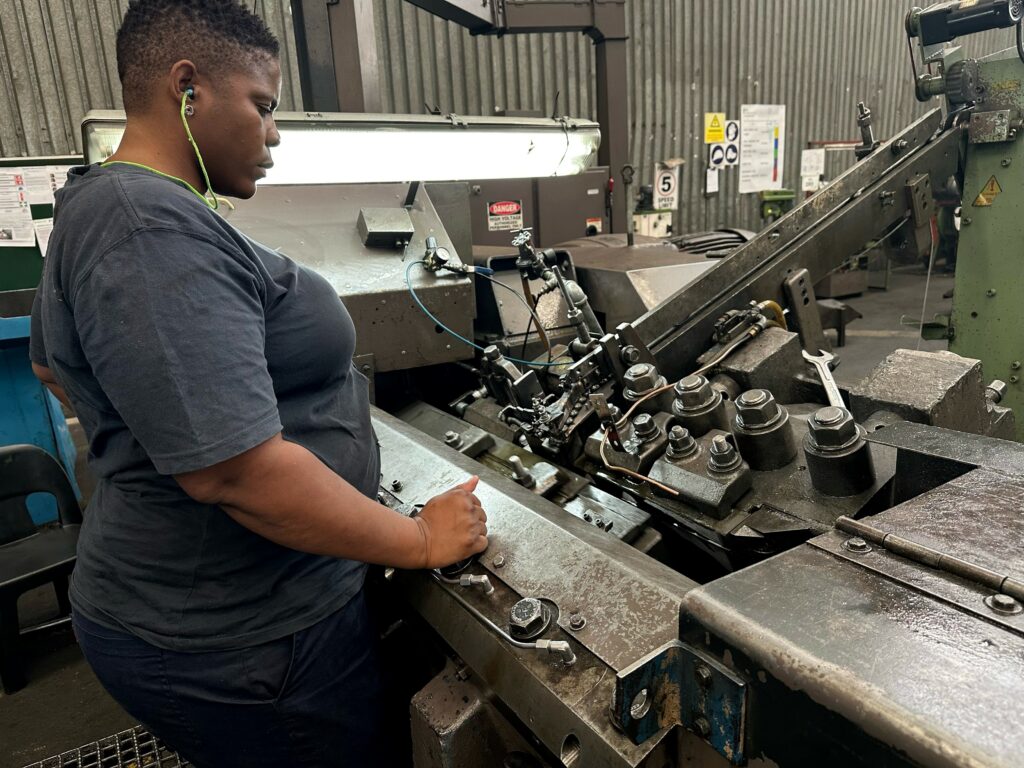
Derek Cohen, the Managing Director of Impala Bolt and Nut, explained, “Tooling for cold forge manufacture of bolts was previously imported, due to lack of skills, plant and equipment.” A significant need, therefore, exists for Impala to have the ability to design and manufacture its products without sourcing tooling from international suppliers.
Through the intervention of the AISI, the company has successfully expanded its in-house capabilities and can now produce tooling locally, eliminating the need for imports. Cohen added, “Working with the AISI has been an incredibly rewarding and enlightening experience. They have added tremendous value by acting as a sounding board and making constructive suggestions.”
Impala Bolt and Nut approached the AISI in response to an expression of interest advertisement on the AISI website. “After initial contact with the AISI, we formed a project team to discuss the opportunity and align it with the company’s objectives. As a team, we brought the project to fruition, successfully investing in new plant and equipment, employing staff, substituting local manufacture for historical imports, developing highly specialised skills, and ultimately facilitating the possibility of future finished product exports,” he further explained.
During the project, Impala’s locally developed products underwent validation by automotive clients representing the original equipment manufacturers. As a result, these products now qualify for local manufacturing, and Impala can produce large quantities to meet their customers’ needs. Within six months of the project’s start, Impala managed to secure, commission and conduct skills transfer of tooling manufacturing capabilities. The company has 104 employees, and the project is expected to be completed in three months. The company looks forward to providing exceptional service to local and international clients.